I worked closely with Seitu Jones as studio assistant during the summer of 2019. I headed production for his Turnip Greens public art proposal at the Nashville Farmers’ Market.
I am so grateful to have had the pleasure of working with his studio, Shannon Brunette, assistance from Charlotte Richardson-Deppe, and Heather Doyle at Chicago Avenue Fire Arts Center in Minneapolis.
This project involved computer aided design, auto body hammer techniques, aluminum welding, plasma cutting, techniques learned in sign and prop-making, and a good bit of teamwork.
Source Material
I worked off of Seitu’s public art proposal documents, attempted a few different approaches, and researched potential processes that would fit criteria of longevity, durability, and physical weight. Bending ply, armatures for stretched canvas, and sheet metal were considered. Aluminum sheet offered the best combination of appearance and durability.
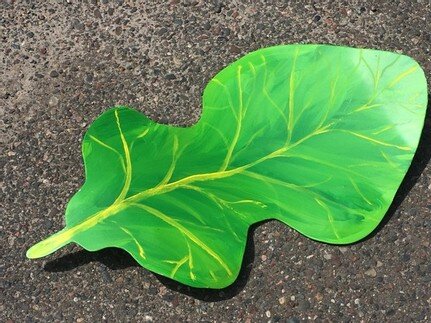
Prototyping and Templating
I took Seitu’s sketchup models and dimensioned them in Rhino. Since the leaves had compound curves, I made a small paper model to simulate sheet bending processes and welding. A small sample was made with a sandbag and set of forming hammers.
Using the grid in Rhino’s interface, I manually enlarged the digital drawings by translating them onto underlayment paper. I drew a scaled grid on the paper and interpreted the digital drawing to form my cutting templates/stencils. Leaves with compound curves were cut and traced twice and cut to find the right seam.
Fabrication
With technique developed and templates made, I began full scale production at Chicago Avenue Fire Arts Center. Over two months, I produced 18 leaves. This involved cutting, shaping, welding, and paint prep. I also hired on Charlotte Richardson-Deppe, a friend from undergraduate studies, and taught her to use a plasma cutter, spool welder, pneumatic tools, and prep metal for painting.
Seitu’s project can be seen on his website or in person at the Nashville Farmer’s Market.